鈦無縫管材的軋制方法及注意事項有哪些?
鈦無縫管材的軋制一般采用往復式(即皮爾格式)冷軋管機進行加工,加工過程中一般采用兩輥(LG)和多輥(LD)軋機進行多道次軋制。鈦管材在變形過程中隨著軋機的回轉以及送進,逐漸進行減壁、減徑,單位長度的管材在一個軋制道次中一般經過5~10次軋制、精整才能獲得工藝要求的管材尺寸規(guī)格。冷軋管機可進行大減徑、減壁加工,但是軋制后尺寸精度較低,管端部易出現(xiàn)開裂、凹凸不齊等現(xiàn)象,對于開裂現(xiàn)象,主要通過管坯加工前修磨、平齊等方法可解決;對于出現(xiàn)的管端不齊,類似“魚嘴”狀現(xiàn)象,在后續(xù)加工過程中需進行平頭處理,否則會造成插頭悶車事故,因此,本文從工藝、工模具、設備等方面進行分析,旨在找出引起管端凹凸不齊的原因,采取有效措施進行解決。芯桿與芯桿小車連接處花鍵間隙過大及由此導致的芯棒位置嚴重移位是造成此次管坯軋制后管材端部凹凸不齊的主要原因。
純鈦管經過開坯軋制時,在一個道次內一般要經過多次精整,軋成需要的鈦管規(guī)格后,管材端部一般會出現(xiàn)1~2mm的輕微的起伏。該批鈦管在原材料及工藝方面與之前生產的管材無差別,但是出現(xiàn)較為嚴重的凹凸起伏現(xiàn)象,長度達70mm,占管材長度的1%,從加工前后外徑及壁厚測試結果來看,試樣壁厚的波動較大,凸部位測量數(shù)據(jù)平均壁厚2.33mm,凹部位測量數(shù)據(jù)平均壁厚2.60mm,兩者壁厚差值達到了0.27mm,而正常軋制后的鈦管端部壁厚偏差為0.05~0.10mm,壁厚的偏差必然引起延伸系數(shù)的不同,可以說端部管材軋制時減壁量的不均是造成管端頭不齊的直接原因,因此,造成管端凹凸不齊可能是設備或工模具所致。
由工模具引起的壁厚不均有齒輪齒條的安裝、模具的對正、模具開口度等因素。經過測量,上下模具孔型的開口度相差0.05。;塞尺測量孔型間隙0.05mm,齒輪與齒條間隙約1.6mm;齒條在機架上固定無松動現(xiàn)象,定位塊無變形;孔型左右錯位切.02mm,零線對齊。以上測量數(shù)據(jù)表明,模具的安裝均在設計要求范圍內。由設備原因引起的壁厚不均有送進量、回轉角度、動作的協(xié)調性等原因。軋制車速及送進量按照工藝要求執(zhí)行,設備運行過程中,在后死點回轉及送進,在前死點回轉,動作協(xié)調,未發(fā)現(xiàn)回轉送進動作提前及滯后的現(xiàn)象;在設備設計要求范圍之內;繼續(xù)測量軋制時的送進量,發(fā)現(xiàn)送進量均勻,但是發(fā)現(xiàn)鈦管在送進時,與管坯同軸的芯桿前后竄動較大,達到了10mm,按照要求芯桿在軋制時的前后竄動量不應該大于0.5mm,否則會嚴重影響軋制時的芯棒位置的準確性,進一步檢查發(fā)現(xiàn)芯桿與芯桿小車連接處花鍵間隙為20mm,超出間隙8mm的要求。當鈦管材在后死點送進時,由于花鍵與芯桿間隙過大,必然導致鈦管坯前進時芯桿也在前進,這樣在軋制時與芯桿相連接的芯棒的位置發(fā)生了較大的變化,即:芯棒與孔型的位置不再是工藝設定的位置,而是前移。這樣當軋制到前死點時,管材實際上被軋到較薄的尺寸;但是雖然芯桿在跟著管坯往前走,花鍵前端的彈簧此時卻一直受力,當孔型走到前死點時,管材的內孔與芯棒脫開,此時彈簧將芯桿后推,這樣芯棒也后退,此時孔型對鈦管軋制后的側邊壁厚較厚的部位進行均整,但是由于芯棒的后退,該均整的壁厚較厚的部位卻未均整,于是造成了壁厚的較大差異。調整芯桿與芯桿小車連接處花鍵間隙,通過調整后,發(fā)現(xiàn)管端頭不齊現(xiàn)象消失。
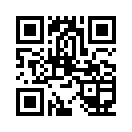